Micro Reaction Process
Our work focused on two main topics in green chemistry : (i) the use of novel reaction media, such as fluorous solvents and ionic liquids, replacing harmful organic solvents and (ii) microflow reactors, and replacing traditional batch reactors. The ultimate goal of organic synthesis is to build up organic molecules beneficial for the better human life and this requires environmentally benign protocols with maximum reaction efficiency. The other question to ask ourselves is if chemical production has to be a matter of big companies, which can afford expensive huge chemical plants. In 20th century the answer is yes, but we do not know in 21st century. Silkworms produce natural silk which we need without becoming gigantic silkworms.
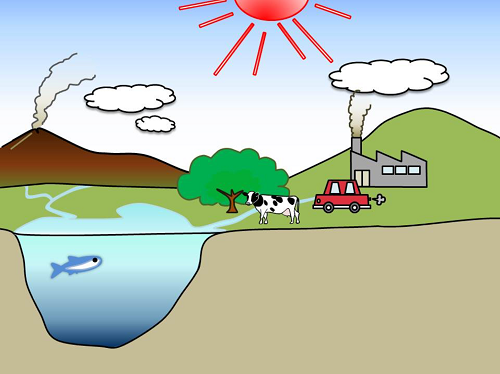
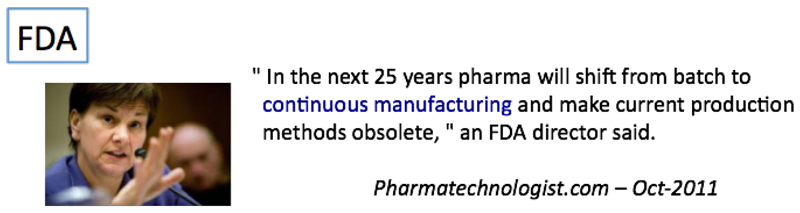
The following figures tell us the superiority of micro space to larger reaction space. Key issue here is extremely high surface to volume ratios for micro space, which bring about advantages to both molecular and heat diffusions. As for our earlier efforts as well as the basic concept we wrote an account covering our research up to 2008, which counts more than 300 citations: Fukuyama, T.; Rahman, M. T.; Sato, M.; Ryu, I. Synlett 2008, 151-163.
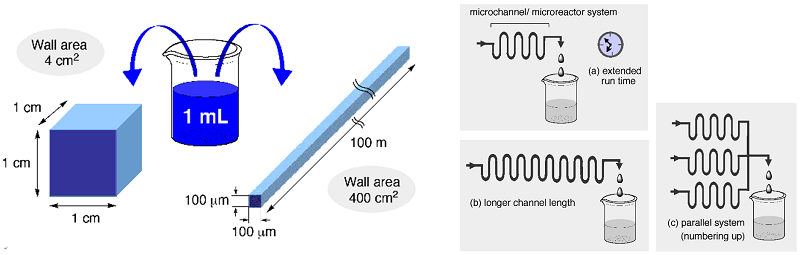
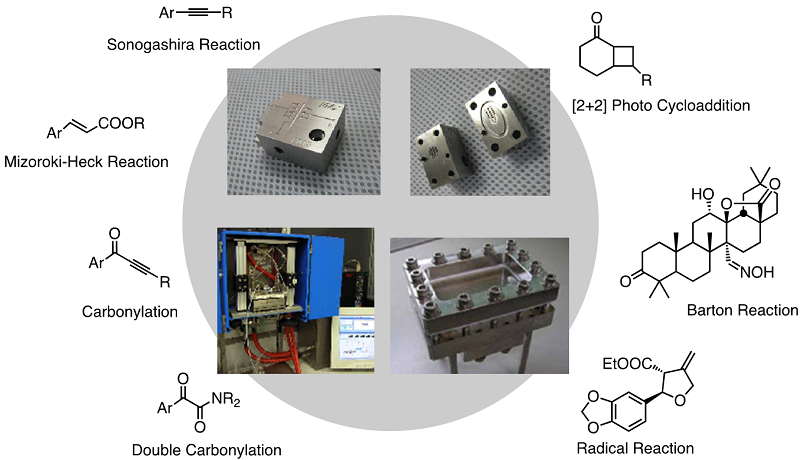
We then tackled gas/liquid biphasic flow reactions. Especially we have undertaken the flow update of carbonylation reactions using CO gas. We all tested flow carbonylation using a variety of reactive intermediates such as acyl anions, acyl cations, acyl radicals, and acyl palladium complexes. Indeed, all suit continuous flow reactions. We published a review on the flow carbonylation in 2014: Fukuyama, T.; Totoki, T.; Ryu, I. Green Chem. 2014, 16, 2042. cited: 100.
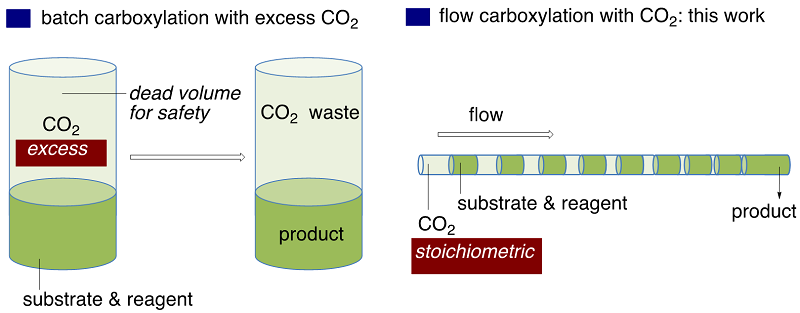
In the gas/liquid biphasic reactions, the large gas-liquid interfacial area is ensured irrespective of the flow mode being gas-liquid segmented flow or annular flow. In the above Scheme, another advantage of flow gas-liquid reaction is illustrated. For a batch autoclave reaction to be run safely, it generally employs dead volume, which is filled with essentially waste CO2. Since flow reaction in a tiny channel does not require dead space, the use of a near-stoichiometric amounts of CO2 would be possible. We already confirmed the stoichiometric flow carbonylation with CO. In the following two Schemes, we illustrated the use of tube-in-tube reactor, in which in situ formed CO gas by the Morgan reaction permeated through the wall of Teflon AF-2400. the consecutive three-step flow reaction for the control of acyllithiums.
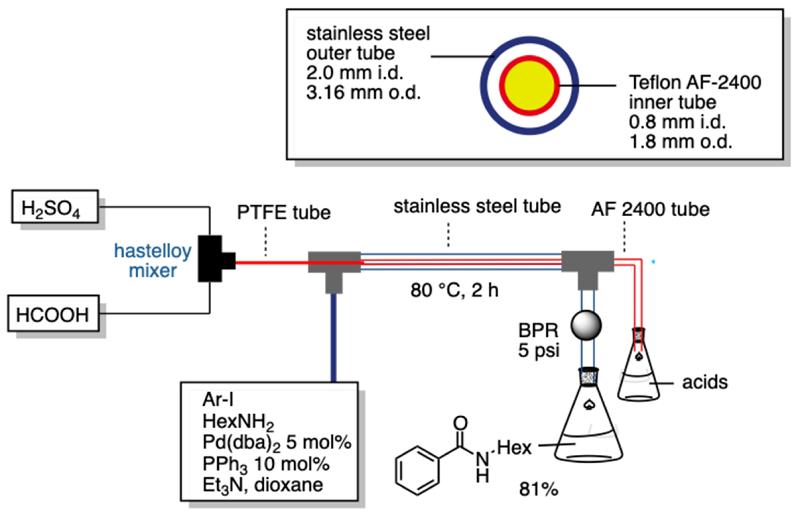
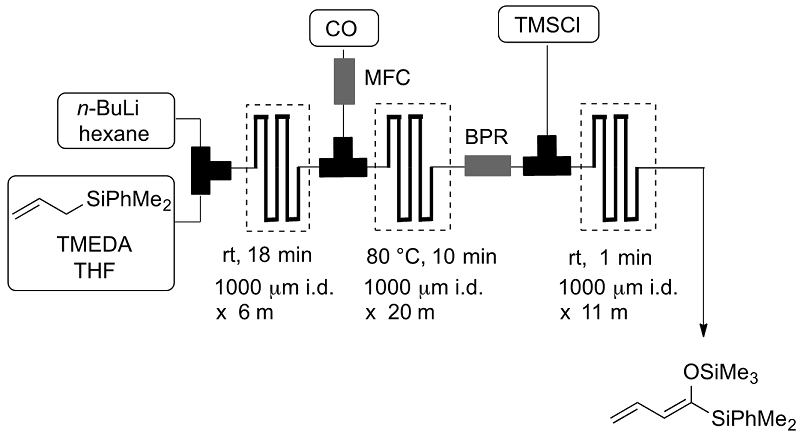
Photochemical reactions have provided many valuable and practical methods for synthetic chemistry. However, photochemical processes using traditional batch reactors generally require a long irradiation time. Such a situation often causes decrease in yield and selectivity due to unfavorable photochemical reactions of the initially formed products. Flow photochemistry received particular attention. Our group also paid attention for the development of useful photoflow reaction tools in a collaboration with MiChS (http://www.michs.jp). The microchannels are designed as the photoreaction suits (MiChS L-1). For Perspective of photoflow chemistry, see: Fukuyama, T.; Kasakado, T.; Hyodo, M.; Ryu, I. Photochem Photobiol Sci. 2022: doi: 10.1007/s43630-021-00151-6.
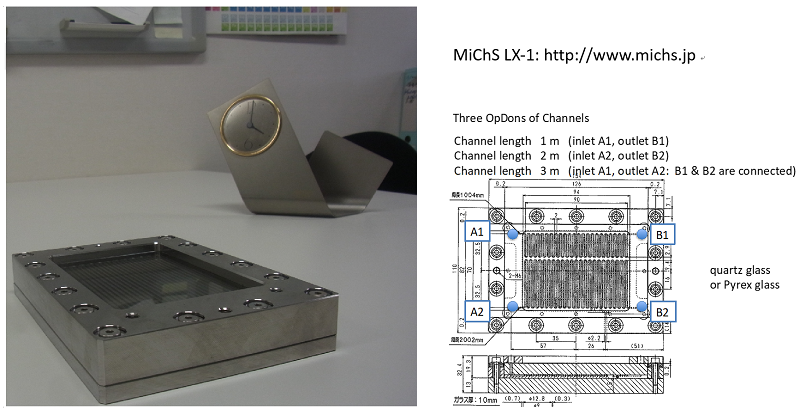
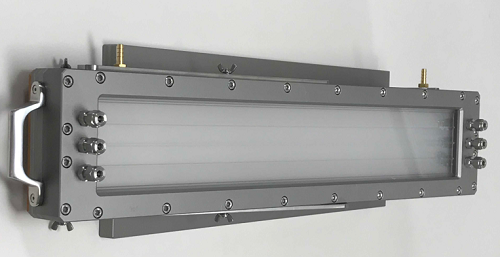
MiChS LX-1: available for gas-liquid biphasic flow reactions under photoirradiation.
For our recent work on flow chemistry, see: a) M. Ueda, N. Imai, S. Yoshida, H. Yasuda, T. Fukuyama, I. Ryu, Eur. J. Org. Chem. 2017, 2017, 6483-6485. b) S. Sumino, M. Uno, T. Fukuyama, I. Ryu, M. Matsuura, A. Yamamoto, Y. Kishikawa, J. Org. Chem, 2017, 82, 5469-5474. c) T. Fukuyama, Y. Fujita, H. Miyoshi, I. Ryu, S.-C. Kao, Y.-K, Wu, Chem. Commun. 2018, 54, 5582 – 5585. d) S. Masui, Y. Manabe, K. Hirao, A. Shimoyama, T. Fukuyama, Takahide, I. Ryu, K. Fukase, Synlett 2019, 30, 397-400. f) S.-C. Kao, Y.-C. Lin, I. Ryu, Y.-K. Wu, Adv. Synth. Catal. 2019, 361, 3639-3644.

The combination of supported catalysts and continuous flow should be the best. In the given example, we reported on two types of flow synthesis of Pristane, which is obtained from basking sharks but taking the basking sharks is banned by the Washington Agreement.
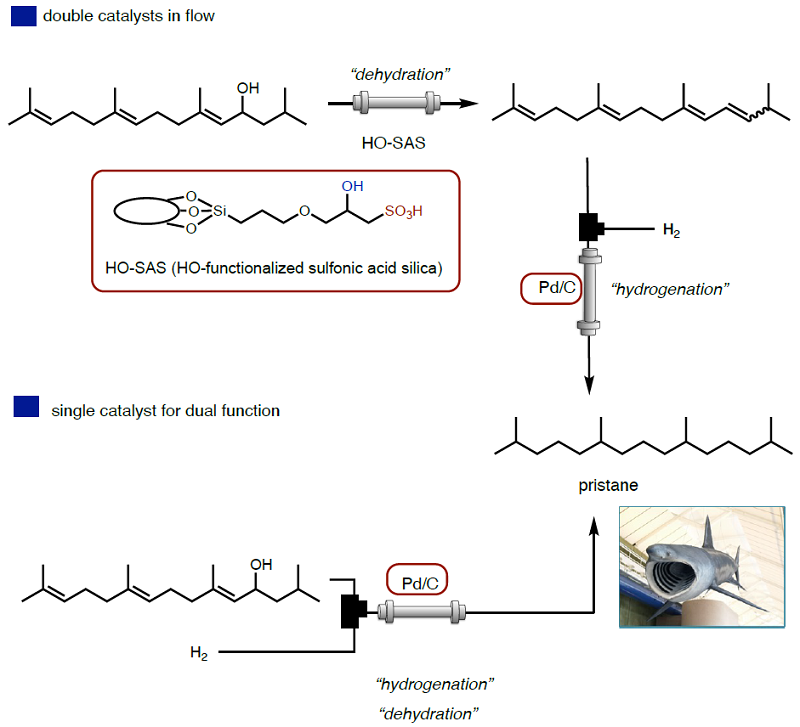
Our group is now challenging organic synthesis in a microdroplet. Join us in drawing straight green lines from lab work to chemical production. Keep in mind that only human beings are the creature of this planet who had used a large-scale production thus far. This would be or has to be changed shortly.
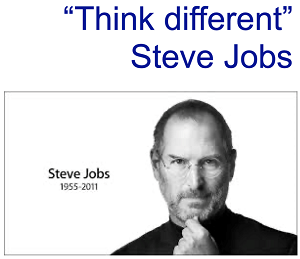
